CONCRETE FORMWORK FOR AN ORGANICALLY SHAPED CONCRETE CEILING
A key architectural feature of the spectacular new building of Frankfurt’s Städel Museum is a large underground exhibition hall with an organically shaped concrete ceiling. Visible to the visitor is a gigantic hilly meadow with 195 circular skylights through which daylight is let in. During the hours of darkness, the lighting in the exhibition hall radiates outwards through the skylights. ACCENTFORM produced the formwork for the concrete ceiling for this architecturally impressive ceiling design.
In order to cast the slab of the approx. 3,000 m² exhibition hall in a three-dimensional geometry, concrete formwork beams are required which reproduce the free-form surface as a negative molded body. ACCENTFORM thus produced 195 shuttering units. The huge ceiling area with the immense height differences presented all those involved with a major challenge. The responsible construction company (ZÜBLIN) therefore decided to concrete the ceiling in five sections: four rectangular sections, each covering one corner of the exhibition hall, and a fifth section covering the central area with its striking hill geometry. Efficient and professional: The division into these five concreting sections meant that the formwork beams could be reused up to four times. Other important criteria in the production of the concrete formwork beams, which consist of a milled upper structure and a standardized substructure, were above all: the lowest price per square metre, high dimensional accuracy as well as smooth and pressure-resistant surfaces.
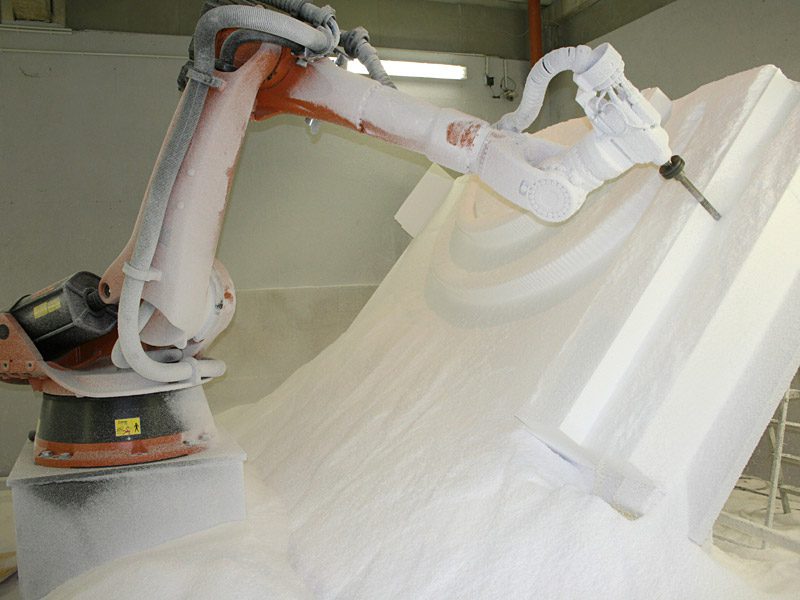
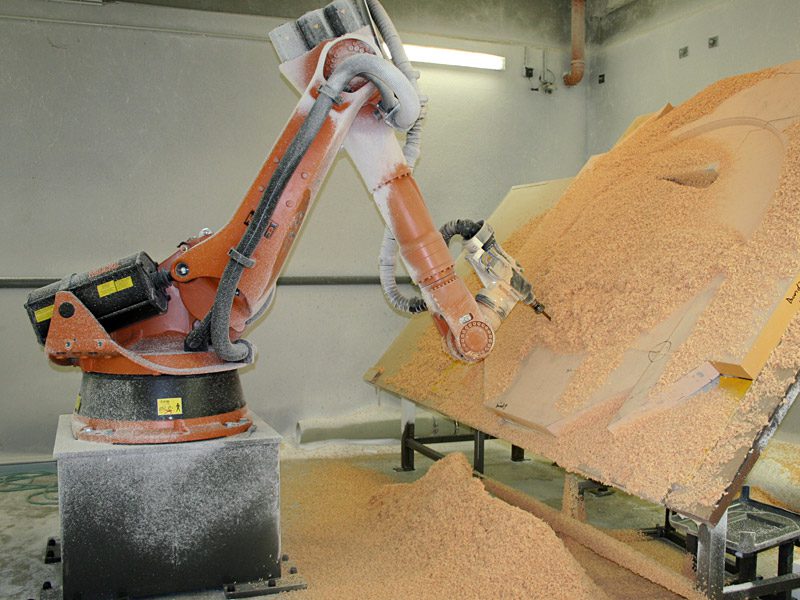
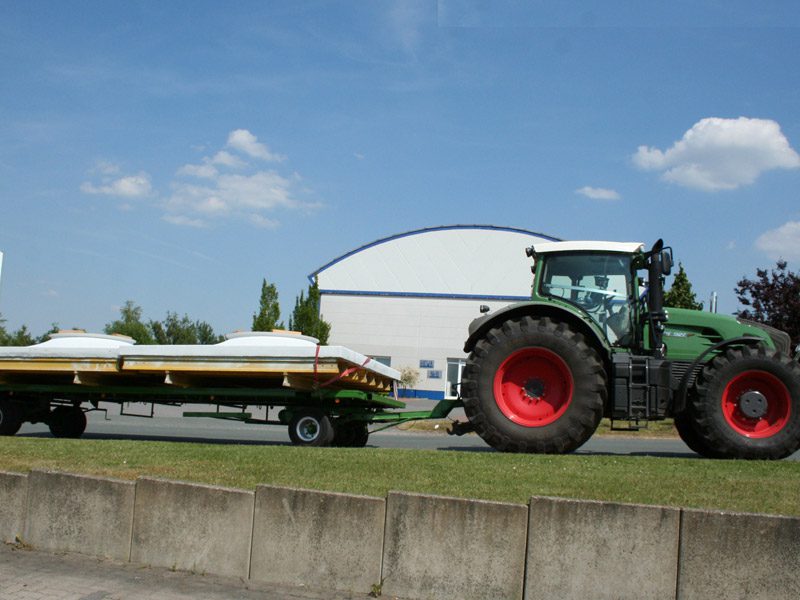
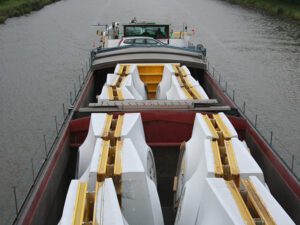
Production of the formwork beams
The substructure consists of a 2 cm thick three-layer formwork panel, each reinforced with 10 formwork beams (type VT20). CNC-machined PS rigid foam blocks (STYROPOR) were then glued onto these. The use of PS rigid foam not only ensures price advantages over other materials, but also guarantees visible success in ceiling design thanks to its high compressive strength (200 KPa). In addition, the use of a robot (KUKA KR 150) for CNC milling the three-dimensional surface proved to be extremely economical.
The PS rigid foam had to be professionally sealed to ensure a good exposed concrete quality and at the same time guarantee a high compressive strength of the surface. For this purpose, an approx. 5 mm thick GRP laminate was applied, which was then leveled and sealed with a topcoat. This technique ensures a reproducible smooth surface for all subsequent formwork oil treatments.
Everything from a single source
Prompt, comprehensive and efficient: ACCENTFORM offers its clients a well thought-out and reliable all-round service from a single source. Approx. 700 m³ of STYROPOR and approx. 12,000 kg of GRP were processed within 3 months. Nevertheless, a concrete formwork beam, including the timber substructure, weighed only 300-400 kg. Due to the size of the component, road transportation would only have been possible as an expensive special transport, so we opted for an inland waterway delivery. With one shipload, up to 48 segments could be transported directly to the construction site of the Städel Museum on the Main – effectively, quickly and inexpensively.
Photographer:
Norbert Miguletz
studio@miguletz.de
www.miguletz.de
Project details for the formwork of the concrete slab
Customer
Städel Museum
Städelsches Kunstinstitut
Dürerstrasse 2
60596 Frankfurt/Main
www.staedelmuseum.de
Realized by
Ed. Züblin AG
Stuttgart head office
Albstadtweg 5
70567 Stuttgart
www.zueblin.de
Our partner
BBS Schalungsbau GmbH
Industriestrasse 21
67240 Bobenheim-Roxheim
Design from
schneider + schumacher
www.schneider-schumacher.de
Project number
P20-11 P20-12