Manufacture of domes, cupolas, radomes of all sizes
ACCENTFORM is a specialist in the manufacture of radomes, large-format spheres, projection domes for simulators or domes
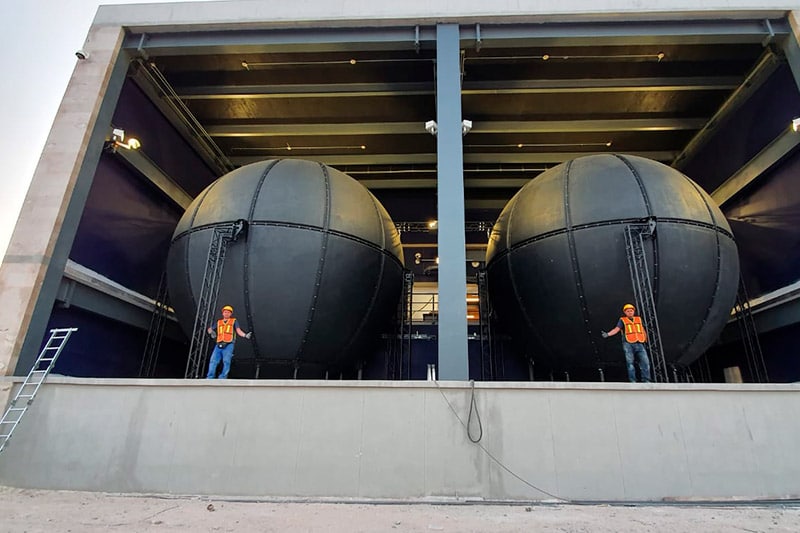
In a projection dome, video recordings, animations or images are projected onto the inside of the spherical surface (dome, spherical section, curved screen). Planetariums are a well-known example. For this purpose, the surface must be smooth and white in color.
A radome (radar dome) is an enclosed shell for measurements or data transmissions. This protects the antennas and sensitive measuring devices from external weather influences. GRP and CFRP are ideal materials for the production of such objects.
Basically, the aim is to produce large-format segments so that as few joints and seams as possible are visible. At the same time, large-format segmentation reduces installation time. The width dimension is limited by the standard transport width (truck width 2.5 m). This results in standard surface areas of approx. 10 m².
Before a segment can be made from GFRP or CFRP, a production mold must be created. Due to the three-dimensional geometry, it makes the most sense for this large production form to have a stable substructure (timber frame construction). Large-format STYROPOR blocks are then glued onto this substructure. It is a very economical material and can be milled very well. Nevertheless, STYROPOR has a very poor surface quality after processing and is not pressure-resistant. The polystyrene structure is therefore milled to an undersize of 12 mm. A special epoxy paste is then applied to the pre-milled surface. This paste hardens within 24 hours and is then milled to the desired dimensions. The resulting surface is hard and can be sanded and painted to a finished state. This makes it suitable as a form of production.
The individual segments for a dome can then be molded from this large-format production mold. First, a gelcoat with a layer thickness of approx. 0.7 mm is applied to the production mold. The glass fiber-reinforced plastic is then laminated on. The layer thicknesses vary between 4 – 8 mm depending on the application. If higher demands are placed on the object (dynamic dome), a sandwich structure is used.
The individual segments of a dome are fastened or glued to the flange at the location using a screw connection.
Pictures from the production:
Reference projection dome
Project details on the production of domes, cupolas, radomes
Project number
P20122
P18049
P19064
P17006